|
|
|
|
DESALINATION PLANTS |
|
Technology
Desalination is a process that removes dissolved minerals (including but not limited to salt) from seawater, brackish water, or treated wastewater. A number of technologies have been developed for desalination, including reverse osmosis (RO), distillation, electrodialysis, and vacuum freezing. Two of these technologies, RO and distillation, are being mostly considered by municipalities, water districts, and private companies all over the world These methods are described below.
Reverse Osmosis (RO)
In RO, feedwater is pumped at high pressure through permeable membranes, separating salts from the water (Figure 1). The feedwater is pretreated to remove particles that would clog the membranes. The quality of the water produced depends on the pressure, the concentration of salts in the feedwater, and the salt permeation constant of the membranes. Product water quality can be improved by adding a second pass of membranes, whereby product water from the first pass is fed to the second pass.
Figure 1. Flow Diagram of a reverse osmosis system
|
|

|
|
Distillation
In the distillation process, feedwater is heated and then evaporated to separate out dissolved minerals. The most common methods of distillation include multistage flash (MSF), multiple effect distillation (MED), and vapor compression (VC)
Input Water (Feedwater)
Desalination plants may use seawater (directly from the ocean through offshore intakes and pipelines, or from wells located on the beach or seafloor), brackish groundwater, or reclaimed water as feedwater. Since brackish water has a lower salt concentration, the cost of desalting brackish water is generally less than the cost of desalting seawater. Intake pipes for desalination plants should be located away from sewage treatment plant outfalls to prevent intake of discharged effluent. If sewage treatment discharges or other types of pollutants are included in the intake, however, the pre- and post-treatment processes should remove the pollutants.
Product Water
Distillation plants produce a high-quality product water that ranges from 1.0 to 50 ppm tds, while RO plants produce a product water that ranges from 10 to 500 ppm tds. (The recommended California drinking water standard for maximum tds is 500 mg/L, which is equivalent to 500 ppm.) In desalination plants that produce water for domestic use, post-treatment processes are often employed to ensure that product water meets the health standards for drinking water as well as recommended aesthetic and anti-corrosive standards.
Desalination product water may be used in its pure form (e.g., for make-up water in power plant boilers) or it may be mixed with less pure water and used for drinking water, irrigation, or other uses. The desalinated product water is usually more pure than drinking water standards, so when product water is intended for municipal use, it may be mixed with water that contains higher levels of total dissolved solids. Pure desalination water is highly acidic and is thus corrosive to pipes, so it has to be mixed with other sources of water that are piped onsite or else adjusted for pH, hardness, and alkalinity before being piped offsite.
Product Water Recovery
The product water recovery relative to input water flow is 15 to 50% for most seawater desalination plants. For every 100 gallons of seawater, 15 to 50 gallons of pure water would be produced along with brine water containing dissolved solids. A desalination plant's recovery varies, in part because the particulars of plant operations depend on site-specific conditions. In several locations in California, pilot projects are being proposed to test plant operations before full-scale projects are built.
Pretreatment Processes
Pretreatment processes are needed to remove substances that would interfere with the desalting process. Algae and bacteria can grow in both RO and distillation plants, so a biocide (usually less than 1 mg/L chlorine) is required to clean the system. Some RO membranes cannot tolerate chlorine, so dechlorination techniques are required. Ozone or ultraviolet light may also be used to remove marine organisms. If ozone is used, it must be removed with chemicals before reaching the membranes. An RO technology has been developed recently that does not require chemical pretreatment.
In RO plants, suspended solids and other particles in the feedwater must be removed to reduce fouling of the membranes. Suspended solids are removed with coagulation and filtration. Metals in the feedwater are rejected along with the salts by the membranes and are discharged in the brine. With normal concentrations for metals in seawater, the metals present in the brine discharge, though concentrated by the RO process, would not exceed discharge limits. Some distillation plants may also need to remove metals due to potential corrosion problems.
Filter Backwashing, Membrane Cleaning and Storage, Scaling Prevention and Removal, and Pipeline Cleaning
The filters for pretreatment of feedwater at RO plants must be cleaned every few days (backwashed) to clear accumulated sand and solids. The RO membranes must be cleaned approximately four times a year and must be replaced every three to five years. Alkaline cleaners are used to remove organic fouling, and acid cleaners are used to remove scale and other inorganic precipitates. All or a portion of RO plants must be shut down when the membranes are replaced. When RO plants are not used continuously, the RO membranes must be stored in a chemical disinfection/preservation solution that must be disposed of after use. Distillation plants can also be shut down for tube bundle replacement, which is analogous to membrane replacement.
Desalination plant components must be cleaned to reduce scaling-a condition where salts deposit on plant surfaces, such as pipes, tubing or membranes. Scaling is caused by the high salt concentration of seawater and can result in reduced plant efficiency and corrosion of the pipes. In general, scaling increases as temperature increases; thus scaling is of greater concern for distillation plants, since RO plants require lower temperatures to operate. Scaling can be reduced by introducing additives to inhibit crystal growth, reducing temperature and/or salt concentrations, removing scale-forming constituents, or seeding to form particles. Once scales have formed, they can be removed with chemical or mechanical means.
In addition to scaling, both RO and distillation plant intake and outfall structures and pipelines can become fouled with naturally occurring organisms or corroded. Structures and pipelines may be cleaned by mechanical means or by applying chemicals or heat. Feedwater may also be deaerated to reduce corrosion.
Waste Discharges
Desalination plants produce liquid wastes that may contain all or some of the following constituents: high salt concentrations, chemicals used during defouling of plant equipment and pretreatment, and toxic metals (which are most likely to be present if the discharge water was in contact with metallic materials used in construction of the plant facilities). Liquid wastes may be discharged directly into the ocean, combined with other discharges (e.g., power plant cooling water or sewage treatment plant effluent) before ocean discharge, discharged into a sewer for treatment in a sewage treatment plant, or dried out and disposed of in a landfill. Desalination plants also produce a small amount of solid waste (e.g., spent pretreatment filters and solid particles that are filtered out in the pretreatment process).
Energy Use
The energy used in the desalination process is primarily electricity and heat. Energy requirements for desalination plants depend on the salinity and temperature of the feedwater, the quality of the water produced, and the desalting technology used.
In addition to electricity requirements, some plants also use thermal energy to heat feedwater. (Because of the inefficiency of converting thermal energy to electricity, there is a high energy "penalty" if electricity is used to heat feedwater. The energy use of a small- to medium-sized industrial facility (such as a large refinery, small steel mill, or large computer center) which uses 75,000 to 100,000 kWh/yr.
Both RO and distillation plants can benefit from cogeneration plants to reduce energy use. Since increased energy use may cause adverse environmental impacts, the individual and cumulative impacts of energy use and production at a proposed desalination plant will require case-by-case analysis.
Comparison of Distillation and Reverse Osmosis Technologies
One advantage of distillation plants is that there is a greater potential for economies of scale. Distillation plants also do not shut down a portion of their operations for cleaning or replacement of equipment as often as RO plants, although distillation plants can and have shut down for tube bundle replacement and cleaning. Pretreatment requirements are greater for RO plants, because coagulants are needed to settle out particles before water passes through the membranes. Unlike RO plants, distillation plants do not generate waste from backwash of pretreatment filters.
Advantages of RO plants over distillation include: RO plant feedwater generally does not require heating, so the thermal impacts of discharges are lower; RO plants have fewer problems with corrosion; RO plants usually have lower energy requirements; RO plants tend to have higher recovery rates-about 45% for seawater; the RO process can remove unwanted contaminants, such as trihalomethane-precursors, pesticides, and bacteria; and RO plants take up less surface area than distillation plants for the same amount of water production. |
|
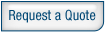 |
|
|
|